
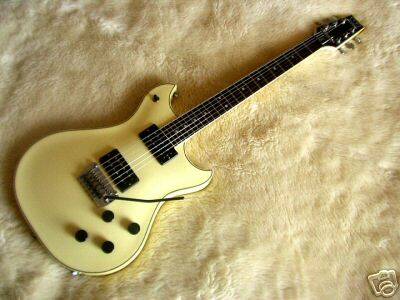

I have mentioned in the Westone Thunder rebuild series that my other hobby is building model cars. The scratchplate damage is the other main issue with this guitar, but it is fixable with no huge chunks missing just a split below the bridge and a little piece gauged out. I was lucky, none of the marking was so deep that it couldn’t be sanded out, and after an hour or two I had a pristine body, looking as good as the day it was cut! The grain is very attractive, with some darker marks behind the bridge area which look like scratches, but and just part of the natural colouring of the Alder body. This lead to a hot sweaty Sunday afternoon with an array of different types of sandpaper and a sanding block to remove all traces of the old finish and the blemishes. As the wood will be on display under a few coats of wood oil, the base has to be as perfect as possible. Unlike a painted finish, it isn’t possible just to sand back the top coat and use wood filler to fill any blemishes. The original body finish was a pale, yellowy clear lacquer which suited the look of the guitar, but now has some quite deep scratches and dents on the front, back and upper horn (see pic). A park now exists on these sites and a marble sculpture in the shape of a guitar marks the place where the entrance of the factory stood (see picture below).As I said in part one of the Westone Cutlass rebuild, I have decided not paint this guitar, but to keep it natural looking. The factory closed in 1987 and was demolished a few years later. Matsumoku was responsible for production in the ’70s and’ 80s for many brands of electric guitars such as Aria, Electra, Epiphone, Fantom, Greco, Ibanez, Skylark, Vantage, Washburn, Westone and Univox. He learned the art of carpentry with Harayama and he was the one who projected most of Matsumoto Mokkou / Matsumoku’s electric guitars in the 60s and 70s. At first, he was hired as a guitar designer. Another key Matsumoto Mokkou / Matsumoku employee was Mr. Harayama also made and distributed guitar necks under his own brand called Jaramer. He was a master craftsman also known for having been responsible for producing guitar bodies and necks for the ESP, Kramer, Schecter and Moon brands. One of them was Norikatsu Harayama, chief engineer in the 1960s. Matsumoto Mokkou has employed excellent engineers, designers and craftsmen. Matsumoto Mokkou also started making his own guitars for export. In 1965, Matsumoto Mokkou started making guitars for various brands like Arai, Colombia and Victor. This commercial relationship between Fujigen and Matsumoto Mokkou, both based in Matsumoto, will last for a few years. All conditions were in place for Matsumoto Mokkou to start making guitars, and in 1962, Fujigen’s founder, Yuichiro Yokouchi, set up a partnership with Matsumoto Mokkou to make electric guitars. But Matsumoto Mokkou was a modern factory with good financial management, a real commercial vision and it had excellent wood drying facilities. In the early 1960s, Matsumoto Mokkou lost competitiveness in foreign markets and Singer Company decided to end their collaboration. As a subsidiary of Singer Sewing Machine Company, Matsumoto Mokkou’s core business was the manufacture of wooden cabinets, tables and accessories for sewing machines. This company specialized in carpentry and was working in its early days for Singer Japan.īeing one of the best carpentry companies in Japan, Matsumoto Mokkou / Matsumoku will soon have an important role in the history of Japanese guitars. Located in Matsumoto, the name of the factory comes indeed from the combination of the words “Matsumoto Mokkou-jo” (carpentry). Tsukada, in the city of Matsumoto, Japan, and his name was at the time Matsumoto Mokkou until 1971.
